十字柱钢结构工厂化加工技术
新建高铁站房项目下部结构采用框架劲性结构体系,劲性结构钢柱设计为十字型截面,柱脚设计为靴梁式预埋柱脚。钢构件为Q345GJC材质,加工性能较差,且截面较大,靴梁式柱脚焊缝多、板材空间拼接多,加工难度较大。项目通过采用精细化的深化设计管理和现代化的工厂加工管理,通过准备、加工的全工序质量控制,实现了大型复杂钢构件的加工质量控制。
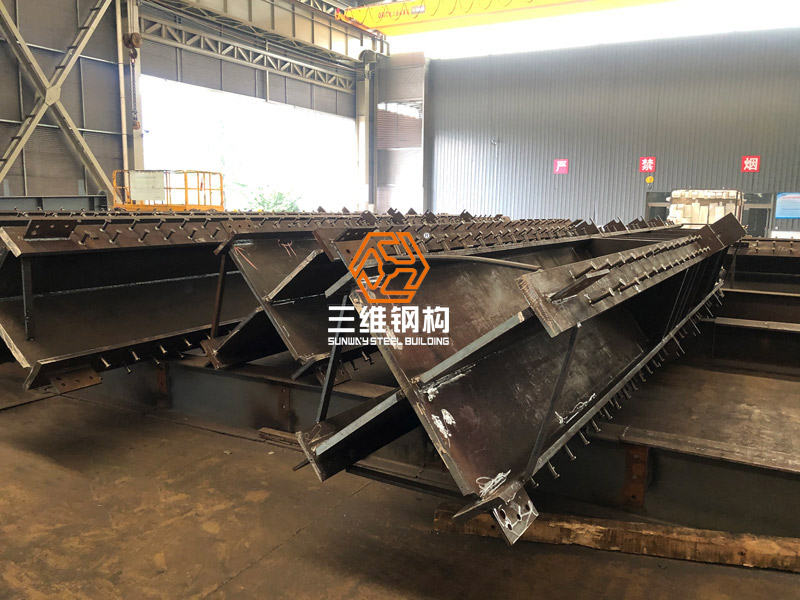
钢结构柱脚上连主体结构,下接下部基础,是决定承载力的主要部位,使上部结构和下部主体有效的连接起来,他能有效固定上部主体的同时将柱子下端的轴力、弯矩和剪力传递给基础,柱脚刚度直接关系到结构的稳定性。同时柱脚上部为十字型钢柱,下部是钢筋混凝土基础,两者结构上存在不连续性。作为结构转接和主要受力构件,如果柱脚及整根钢柱处理不当、加工质量不可靠,将对整体结构造成严重不良影响。
钢结构的加工制造随着结构的发展,钢结构的制造工业机械化水平也在不断提高。从设计入手,结合制造工艺,促进产品的定型化、标准化、系列化,形成加工流水线,促进批量化生产,降低造价。我国钢结构自19世纪开始发展,随着工厂内加工工艺和管理模式的日渐成熟,新型智能化加工设备的推陈出新,复杂钢结构节点的加工质量也到了进一步保障,加工效率大幅提高。
2工厂化加工管理
2.1工艺流程综述
施工准备阶段进行原材料的采购,进厂后进行检验,合格后再进行预处理,审阅施工图后完成工艺准备、焊接工艺评定、制作工藝流程。材料进场后按照图纸尺寸要求进行放样,检查套料的尺寸精度后再进行下料,切割、钻孔、钢材冷热加工成形后再进行尺寸检查,完成焊接、矫正后合拢组装,再进行焊接、矫正,经过初装、中装并逐级检查矫正后,进行大合拢总拼装。在车间完成构建的预拼装,全部检查合格后,对构建进行涂装编号,最终验收,合格后出厂。
靴梁式十字柱结构由1段十字型钢柱及4个靴梁组成,十字型钢柱加工步骤为:先加工出一个H型钢柱,再将两个T型钢柱组装在H型钢柱上,再对端部铣平,验收后分段完成十字柱加工;现场施工靴梁式十字柱节点分五次进行加工,即十字型钢柱和4个靴梁分次加工,在现场进行靴梁和十字柱的焊接,完成靴梁式十字柱结构的制作。
2.2深化设计管理
基于BIM技术,应用Tekla软件,通过对钢结构施工图纸节点的(建模→分析→分解→钢筋-钢构节点深化→焊缝深化→形成三维深化设计成果→导出深化设计图纸→深化设计图纸确认→出加工图→加工)等管理流程,实现对钢结构节点的深化设计,使图纸信息由设计信息完成向加工、安装信息的转化。
工程靴梁式十字柱结构,其靴梁柱脚是深化设计的重点。通过对节点的三维模型搭建,优化钢构-钢筋穿插,确定连接板、预埋螺栓、铆钉等细部构件定位,并输出可用于指导工厂化加工的钢结构加工图。
2.3工厂内工艺管理
(1)下料
钢柱主体按无余量加工形式下料,减少二次切割;构件长4.1m,考虑上端端铣3~4mm以及整体焊接收缩量,翼板下料长度为4105mm,允许偏差±1mm;全熔透区域腹板下料宽度加设2mm焊接收缩余量。
45mm腹板在下料后应先完成制孔,再进行坡口开设;注意坡口正、反向的区别,严格按照工艺文件要求控制坡口角度及钝边尺寸,坡口角度偏差0~﹢5°,钝边尺寸偏差0~-2mm,并处理好半熔透和全熔透焊接坡口的过渡。
(2)制孔
45mm厚腹板Φ22穿筋孔采用高速龙门钻、三维钻(宽≤1220mm)制孔,80mm厚靴梁翼板Φ22穿筋孔亦可采用平面钻制孔。
(3)组立
腹板与翼板焊接连接区域应将铁锈、污垢等清除干净。十字柱中H型及双T型(将两T型腹板位置点焊组成H型)宜采用人工卧式组立,在平整胎架上进行,保证截面尺寸。
引熄弧板材质、厚度、坡口尺寸选用与腹板相同的,保证焊缝端部质量。为减少构件翻身及焊接变形,组立时腹板焊接坡口深坡口应同侧,同时进行深坡口侧的打底焊、填充焊等,翻身后完成浅坡口侧的清根、打底焊、填充焊等。4.1m长首节柱H型重约10t,单个T型重约5t,组立时应加设安全支撑板防倾斜,并对构件吨位及件号进行标识。
(4)焊接
十字柱焊接前预热至80℃;焊接时应注意翻身,减少焊接变形。H型及双T型焊缝应采用埋弧焊盖面,十字焊缝位置空间尺寸约为1m*1m,可采用小车埋弧焊。45mm厚腹板与翼板焊接后,焊缝焊脚高度10mm,允许偏差0~+2mm,不允许加大焊脚高度。
(5)端铣及栓钉焊
采用大型端铣机(4.5米*6米)进行十字柱顶部端铣。 (6)翻身倒运
在翼板对应位置加设翻身吊耳,在翼板外侧加设弧形卡板工装。使用50t桁车主钩、副钩完成构件翻身。
(7)涂装运输
表面处理:
承轨层以下构件均为劲性构件,无需抛丸除锈,但应去除飞溅、油污等杂质,保证构件外观质量。
构件标识:
1)按《工厂构件标识-通用工艺》执行,并贴二维码扫描图片(即BIM条码)。
2)总装车间应在钢柱柱顶往下500mm位置的图纸▲侧,打“△”型的样冲眼标识。油漆车间用白色油漆明显。
2.4厂内加工要求
工厂内加工的基本要求如下:
(1)焊缝要求
1)焊缝要求参照焊缝通图。
2)柱的翼缘板拼接缝和腹板拼接缝的间距不应小于200mm,拼接长度不小于600mm;所有拼接缝都必须避开节点区域、加劲板200mm以上。
3)对接焊缝质量等级均为一级。
(2)材料要求
1)焊材,焊剂在使用前应在350℃烘焙2h。
2)栓钉,受潮的栓钉瓷环使用前应在120℃~150℃范围内烘焙1h~2h。栓钉选用ML15型。
(3)预热要求
板厚≥40mm时,焊缝坡口两侧100mm范围内,焊前应预热到80℃;层间温度控制在80~250℃;焊后用保温棉覆盖缓冷至常温。为避免延迟裂纹产生,构件发货前应再次检查构件焊缝。
(4)其他要求
1)采用火焰校正构件变形,加热校正一般温度为700~800℃,不得超过900℃。
2)过焊孔按照图纸及《天津厂过焊孔-通用工艺》执行;定位焊按照厂通用工艺执行。
3工厂加工质量控制要点
3.1 原材料质量管理
1)物资主管部门在进行工程所需的各种材料的采购前,应审查生产厂家是否满足业主及工程所需材料要求,并要求提供相关证明。必要时应进行材料产地或生产厂家的质量调查,确保工程材料的质量保证。
2)材料进场后,质量主管部门与物资主管部门负责按照材料质量标准进行外观质量和几何尺寸的检验,并做好相关记录。
3)质量主管部门在外观质量检查合格的原材料、半成品中按照业主、监理及国家标准的规定进行取样,抽取的样品由质量主管部门材料检验员负责送检,检测单位应具有规定的资质并在当地建设行政主管部门备案认可。
4)只有经过验收、检验被确认为合格的原材料、半成品、零部件才能被允许使用。
5)经检验不合格的材料应进行明显的标识,并及时与供应商联系按照合同协商解决。严禁在工程上使用不合格材料。
6)材料进场验收后,均应做好标识,并按要求进行保管。
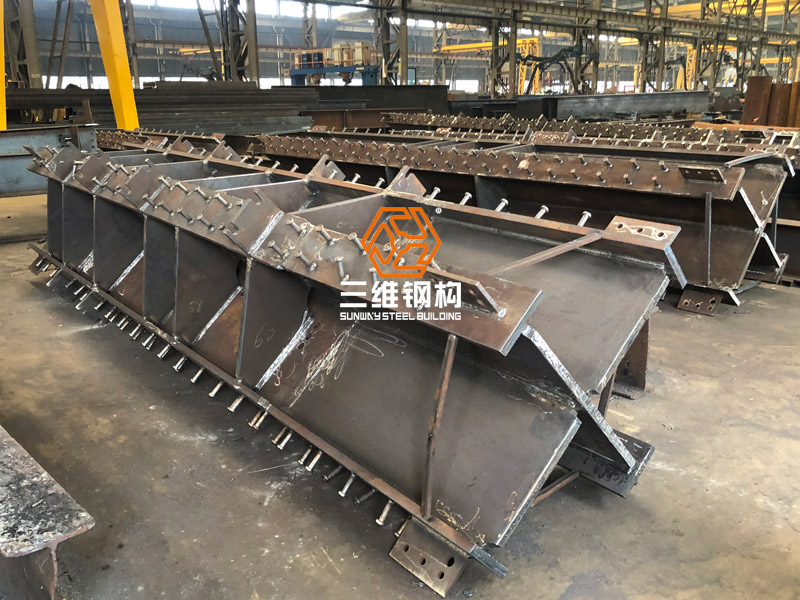
3.2 制作过程的质量控制
1)工程质量检验工作必须严格按照国家和地方政府的法律、法规、规范及规程标准执行。
2)工程開工前,相关部门应对车间及作业班组进行技术、制作工艺和检验计划交底。
3)作业班组应严格按照设计图纸和技术交底、制作工艺以及质量验收规范的要求进行,专职质量检验员应按照检验批的划分随时检查制作质量,发现有不符合验收标准要求的及时进行整改。
4)作业班组在工程生产过程中严格进行“三检制”。上道工序经检验合格后才能进入下道工序的生产。
5)专职质量检验员及车间应认真做好生产记录,以保持加工质量的可追溯性。
3.3 成品保护管理
1)质量主管部门负责监督、检查车间对构件、物资的标识和可追溯性的管理工作。
2)物资主管部门以及车间负责对原、辅材料及生产过程中所有零部件、构件进行标识,并有可追溯性。
3)库内存放物资,物资主管部门宜采用悬挂卡片的方法标识名称、规格、材质、数量、产地等。
4)下料班组在零部件下料完成后,进入下道工序前用油漆标明零件号、材质等信息。
5)每道焊接作业完成后,焊接班组应在焊缝附近标记焊工钢印号。
6)总装班组应在构件组装完成后,用钢印标记出构件编号。
7)成品堆场构件的堆放、发运的质量管理。
8)钢构件制作完毕后应加以临时围护隔离,防止踏踩。
9)构件需要运输时,应注意防止磕碰,防止在地面拖拉。
相关资讯推荐
- 钢结构工程的造价构成有哪些?
- 钢结构加工厂会使用哪些工艺呢?
- 钢结构夹层设计制作安装
- 钢结构加工生产需要哪些专业知识和技能?
- 钢结构加工焊接变形的火焰矫正施工方法
- 建筑钢结构加工的四种主要方法
- 钢结构加工制孔方法的有哪些?
- 钢结构加工焊接缺陷产生的原因和处理办法
- 钢结构加工中边缘加工的方法
- 钢构件的加工质量对于厂房的安装影响?